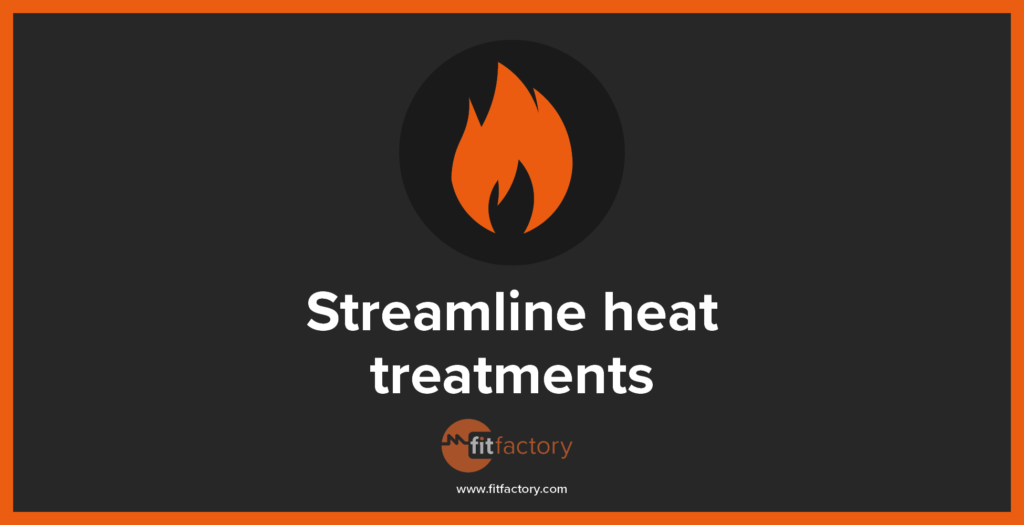
Ten years ago, Apple advertised its newest iPhone model with the slogan, “there’s an app for that.” Since that time, specialised software and apps have proliferated beyond just consumers. Many different manufacturing companies used specialised software for everything from benchmarking to monitoring WIP. But, heat treatment companies that serve the aerospace industry have lagged behind other manufacturing sectors.
Cutting-edge heat treatment technology – manual workflow monitoring
Many heat process companies use cutting-edge technology in their heat lines but still rely on generic MRP systems that aren’t compatible with the heat treatment workflow. Even worse, many firms still use manual workflow monitoring and duplicative data entry.
When a customer calls to check on the status of an order, the front office has to send a runner down to the shop floor to find out where the order is. If the organisation doesn’t have a parts tracking system, it can take hours just to locate where all the parts are in the process.
This wastes time, resources, and invites mistakes. It also makes it difficult to provide exceptional customer service when it takes hours to give a simple status report to the customer.
The sharp technology curve is creating an expectation in customers to be able to get instant answers. Soon, heat treatment companies that are still using manual tracking and workflow monitoring systems will find their aerospace customers are losing patience.
Generic MRP systems don’t work for specialised companies
The solution to the problem seems obvious. Part tracking and workflow monitoring are the perfect tasks for software. But, as every special process heat treatment company can attest, generic MRP systems aren’t designed for the workflow of the industry.
Some companies end up using multiple systems. But, often the different systems don’t communicate with each other, and the administrative staff ends up entering the same data multiple times for each job and part.
Generic MRP systems don’t work for special process companies. That’s why so many still use manual workflow monitoring.
Specialised software for a specialised business
The factory of the future is already here. Smart manufacturing is taking over every sector. The driver of smart manufacturing is smart software. Heat treatment shops don’t have to be left out in the cold. It is no longer the case that ERPs are only for large organisations, and MRP is only for manufacturers. There is now software that is specialised to work with the natural heat treatment workflow. Instead of trying to cobble together a workable solution from multiple pieces of software, businesses can have a Production Control System that works for heat treatment firms without any alterations.
These specialised Production Control Systems allow shops to:
- Track parts from docketing to dispatch
- Accurately measure their capacity
- Optimise the operation of all their heat lines
- Minimise the amount of data entry
- Make it easier to maintain Nadcap & AS9100 certifications
Part tracking from docketing to dispatch
Generic MRP systems want to track inventory, including when the parts arrive to when the final product is sold. But, that’s not workable for special process companies. A specialised Production Control System allows a firm to track a part the moment it arrives from the customer through the different heat lines and post-processes, and it ensures that the right part is shipped back to the right customer.
The right software will tell you at a glance:
- What jobs are being worked on
- When the jobs were started
- When the jobs will be completed
- Who is working on the jobs
- Which heat line every part for every job currently is at
This reduces mistakes with parts from multiple customers that were batched together for a specific oven. It also allows the front office to look at a screen to give an accurate progress report to the customer without having to check with the shop floor.
Accurate capacity management
Seasoned pros are good at estimating shop capacity. But, even experienced heat treatment veterans make mistakes. This results in either late deliveries or wasted capacity. A specialised Production Control System provides you with SFDC and capacity planning. You can quickly see your capacity based on current jobs so that you can give an accurate delivery estimate to the customer.
This not only improves your customer service, but it also prevents you from having idle ovens.
Optimise heat lines – minimise data entry
Heat treatment workflows are too complicated for generic manufacturing software. Many heat treatment companies rely on manual systems to keep track of what parts from what jobs are being batched together in different ovens and different post-processes. Then, workers have to rely on memory or manual systems to make sure the right parts are grouped back together and shipped back to the right customer.
A Production Control System designed for special processes makes the workflow management much easier.
The system can split up jobs and batch parts that need to go into the oven at the same temperature or need the same post-processes applied. It never loses track of where a single part is. The system is smart enough to know where each part of every job is, and which parts need to go back to which customers.
Best of all, you only have to enter the data once.
Maintain Nadcap & AS9100 certifications
It’s impossible to service the aerospace industry as a heat treatment company without obtaining your Nadcap and AS9100 accreditations. However, to obtain accreditation and to maintain that accreditation, requires a significant amount of work. Many companies spend hours dealing with document generation for these accreditations.
A Production Control System makes obtaining and maintaining Nadcap and AS9100 accreditations much easier. The software can produce the records, logs, and other key documentation needed with a few clicks. This saves the typical company hundreds of man-hours over having to manually create all the documentation required by these programs.
Heat treatment companies supplying the aerospace sector don’t have to cobble together multiple MRP systems or rely on manual workflow management. There are Production Control Systems that are aligned with the needs and demands of a special process heat treatment company right out of the box.
Having the right software boosts productivity, reduces administrative costs, and improves customer service. It also allows for more accurate capacity forecasting. If your organisation is not using a specialised Production Control System, you are leaving money on the table.
To learn more about how we can help Heat Treatment Companies improve productivity, please contact us.